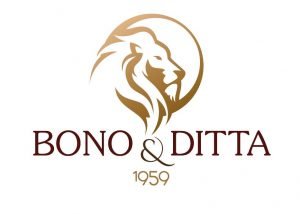
The agri-food sector is extremely important for Italy. In addition to being synonymous with excellence and quality, this sector contributes significantly to the economy, making up 15% of Italy’s GDP.
The wine sector plays a vital role with high added value in history and production, accounting for 10% of the industry.
Today, in our collective imagination, wine is linked exclusively to tradition and ancient knowledge, and many do not consider the digitization and continuous innovation of processes with a focus on sustainability.
This is the case of Bono & Ditta SpA of Campobello di Mazara, a company with ancient roots but a modern and dynamic spirit.
Spread over an area of over 60,000 square meters, Bono e Ditta is internationally known for producing a wide range of products:
- Musts and concentrated musts explicitly used for the production of wines
- Cooked musts used in vinegar factories and for the “Balsamic Vinegars of Modena”
- Grape juices and concentrates used in beverages, the dairy industry, and baby food
The experience gained in more than 60 activities, and continuous research has allowed the company to develop new processes to maintain all the properties of the raw material used, enhancing waste and activating new techniques for the separation and extraction of precious components of grapes, polyphenols, known for their exceptional antioxidant power, in great demand by the cosmetic and nutraceutical industry.
The company has 10,000 square meters of operating facilities with four independent production lines: the musts line, the juice line, the polyphenolic extracts line, and the derivatives and other fruit lines. Additionally, the facilities contain two autonomous aseptic packaging lines.
The plant has a daily production capacity of 3,000 Hl of concentrated juices and musts with an overall storage capacity of nearly 200,000 Hl.
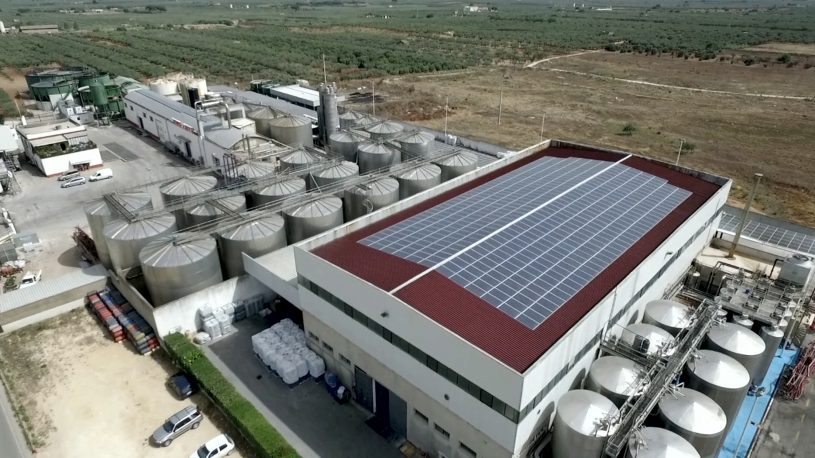
60% of the reference market is Italian, with the remaining 40% made up of the foreign market.
Since February 2022, Bono & Ditta has undertaken the factory digitization process, affecting the production lines and the utility area.
Thanks to Connect IT, Cannon Automata’s digital factory solution, the factory is perfectly integrated into areas subject to digitization, improving interconnection and allowing Bono & Ditta to analyze key indicators in detail by exploiting data analysis to increase its competitive advantage in the market.
Cannon Automata developed and supplied the customized I4.0 integration solution via a local server, allowing correct planning and management of production orders through dedicated dashboards.
The integrated system interfaces with all areas involved in the digitization process. In the thermal power plant, the system communicates with Cannon Bono Energia steam generators based on:
- The type of processing foreseen;
- The indications of the production of steam necessary for the users of the production plant;
- The exchange of production and consumption data, collected by the sensors at the end of the cycle.
The high-tech supply integrates all the standard functions necessary for system control:
- Manifold pressure regulation
- Distribution of the load to increase the overall efficiency of the system
- Alarm control unit
The centralized IT system receives the pressure set point according to the plant’s requirements. This allows efficient load management as it can be changed when more pressure is needed on the machines in the production system, maintaining a lower level when a reduced steam flow is sufficient. Furthermore, depending on the regulation of the pressure set point, the load distribution system sets the pressure set point between the boilers with a rotation criterion, monitoring and recording the data to keep each machine in the realm of maximum efficiency.
Process water sterilization and chlorine abatement system
Through the Totem I4.0 intelligent station, Cannon Automata’s operator interface solution, it is possible to view the planned orders, select the chosen order, and send the start and stop commands for the production processes. Furthermore, the dedicated graphic page displays any anomalies, alarms, and events in the water pre-treatment, process water sterilization, and chlorine abatement systems.
The system reads the temperature, pressure, and flow rate data measured in 3 plant nodes, monitoring efficiency and any anomalies.
Integration of the production line
The areas involved are the must production and treatment plants. In addition to managing the production order, the variables are monitored and stored in the database for subsequent viewing or consultation.
The alarms are also logged in the central database to ensure timely recording of events for each production order.
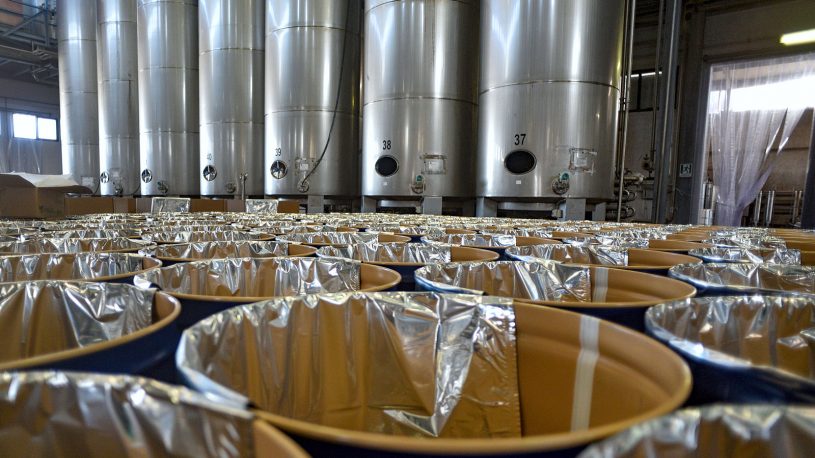