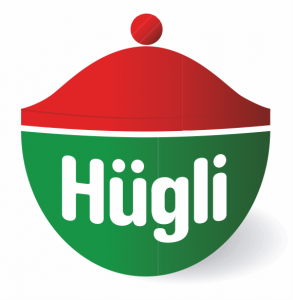
The client
The creation and development of a digital ecosystem have proven decisive for increasing flexibility and production performance, improving the collection and management of data for decision-making purposes.
This case study focuses on Ali-Big srl Industria Alimentare, a company part of Hügli group, specializing in the production and distribution of food products, specifically soups, sauces, broths, condiments, desserts and ready meals.
The challenge
The main goal of the company is to digitize the entire plant, making the information usable at various company levels including top management, quality assurance, production, and maintenance. This digitization integrates a preventive analysis system within the plant, reducing costs, mitigating errors and making operational improvements that allow the factory to meet the daily needs.
The solution
Thanks to Connect IT , The Automata’s global solution for Digital Factory 4.0, it was possible to create a seamless integration among the factory management system, the production lines, quality control assurance, maintenance, auxiliary and utility areas.
The supplied system includes the following solutions that interface at different company levels:
- Plant supervision: a solution that allows you to manage histories and process the information collected through dedicated dashboards, customizing them to the specific needs of the customer and according to the different company area.
- Suite MES: a totally independent MES – Manufacturing Execution System – able to communicate with the management software already present in the company and with the production area in a bidirectional way.
- Operator interface 4.0: the key element found at the production level, essential for bidirectional communication between the MES and the machines.
- Machine Interface 4.0: interfaces with the plant machines for the purpose of compliance with Industry 4.0 requirements.
The areas subject to digitization are:
- Special line
Dedicated to the production of customized products.
- Retail line
Intended for the production of standard products.
- Doypack line
Dedicated to the production of ready meal products.
- Auxiliary services area
Including steam generators, emission monitoring, osmosis and water purification plants, and evaporation towers.
- Utility area:
Control and management of corporate consumption, especially water, electricity and gas.
Let’s analyze in detail the architecture and the process flow:
- The customer manages all information relating to production planning and product information through a management system – developed by Automata – that is integrated with the company’s server.
- The management system interfaces with the production area through Automata’s operator panel, which plays the role of gateway to communicate the production orders. Once the order is received, the panel assigns it to the different machines of the line. By interfacing with the PCL of each machine, it transfers the recipe to be loaded and collects in real-time the production data, process data, KPI data, operators log and equipment status.
- Totem I4.0, located in the production area, displays all information at the line level through dedicated dashboards, and includes information on the auxiliary and utility services.
- The panels, distributed along the production line, are of fundamental use, in fact, they have made it possible to integrate, in digital format, all the quality control activities carried out during the process, generating reports online and in real time. All the reports compiled in this way are stored in the central database, with all the information collected for each product code and for each production batch.
- All information available on the company server can be displayed through dedicated and customized dashboards. The data collected is a key element. In fact, they play a strategic role for the different company areas:
- Top management: the use of main KPIs on production capacity
- Efficiency indicators: primary for the tactical-strategic activities managed at the executive level (OEE, FTE)
- Machine KPIs: meaningful for the quality, maintenance and production areas
- Process indicators: strategic for quality controls (temperature, pH, % of salt, weights, and many others)
The benefits
- Control and management of the entire production process, auxiliary and utility services of the energy area
- Increased production performance
- Increased production flexibility
- Product and process quality improvement
- Reduction of waste and rework
- Collection, historicization and KPI calculation
- Usability of information at different company levels
- Industry 4.0 advantages
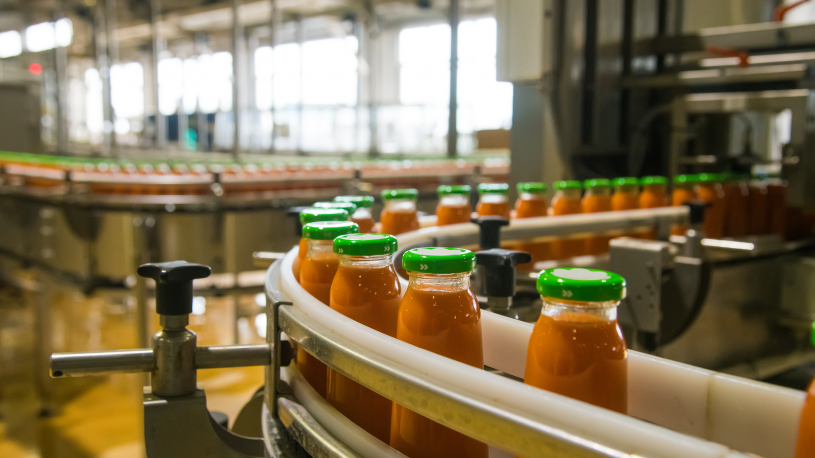