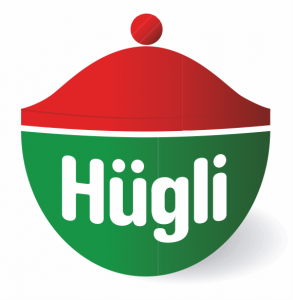
Il cliente
La creazione e lo sviluppo di un ecosistema digitale si è rivelato decisivo per incrementare la flessibilità e le performance produttive, migliorando la raccolta e la gestione dei dati a fini decisionali.
Il protagonista della nostra storia è Ali-Big srl Industria Alimentare, del gruppo internazionale Hügli, specializzata nella produzione e nella distribuzione di prodotti alimentari, nello specifico zuppe, salse, brodi, condimenti, dessert e piatti pronti.
La sfida
L’azienda ha avviato un percorso di trasformazione digitale che coinvolge lo stabilimento produttivo di Brivio integrando l’area utilities ed energia.
L’obiettivo principale dell’azienda è quello di migliorare la produttività, rendere le informazioni fruibili ai vari livelli aziendali, integrare un sistema di analisi preventiva, ridurre i costi, mitigare gli errori e apportare miglioramenti operativi che consentano alla fabbrica di soddisfare le esigenze odierne di flessibilità.
La soluzione
Grazie a Connect IT Fabbrica Digitale 4.0 di Cannon Automata è stato possibile creare una perfetta integrazione tra il sistema gestionale di fabbrica, le linee di produzione, l’area utilities ed energia.
Il sistema fornito comprende le seguenti soluzioni che si interfacciano ai vari livelli aziendali:
- Supervisione impianto: per gestire, storicizzare ed elaborare le informazioni raccolte tramite dashboard dedicate customizzandole sulle specifiche esigenze del cliente e in base alle differenti aree aziendali.
- Suite MES: sviluppo e integrazione di un sistema MES totalmente indipendente, in grado di comunicare con i software gestionali già presenti in azienda e con l’aria produttiva in modo bidirezionale.
- Interfaccia operatore 4.0: elemento chiave a livello d’impianto per una comunicazione bidirezionale tra il MES e le macchine in campo.
- Interfaccia macchina 4.0: Interfacciamento con le macchine dell’impianto e rispetto dei requisiti Industria 4.0.
Nello specifico le aree oggetto di digitalizzazione sono:
- La linea speciale: dedicata alla produzione di prodotti personalizzati sulle specifiche esigenze del cliente.
- La linea retail: destinata alla produzione di prodotti standard.
- La linea doypack: dedicata alla produzione di prodotti a base di riso.
- Area servizi ausiliari destinati alla produzione: comprende generatori di vapore con il monitoraggio emissioni, impianto osmosi e depurazione acqua e la torre di evaporazione.
- Area servizi generali: per il controllo e la gestione dei macro consumi aziendali, nello specifico acqua, energia elettrica e gas.
Analizziamo nel dettaglio l’architettura e il flusso di processo:
- Il cliente gestisce tutte le informazioni relative alla pianificazione della produzione e le informazioni del prodotto nel processo produttivo, attraverso il sistema gestionale sviluppato da Automata e integrato sul server aziendale.
- Il sistema gestionale Automata si interfaccia con l’area di produzione attraverso vari pannelli operatore, sempre prodotti da Automata, che svolgono il ruolo di gateway. Una volta ricevuto l’ordine di produzione dal gestionale, il pannello lo assegna alle diverse macchine della linea Interfacciandosi con il PCL di ogni macchina, trasferisce la ricetta da caricare e raccoglie in tempo reale i dati di produzione, i dati di processo, i KPI, lo storico degli operatori e lo stato delle attrezzature.
- Il Totem I4.0, situato nell’area di produzione, visualizza con cruscotti dedicati tutte le informazioni delle linee, nonché i servizi ausiliari e generali.
- Di fondamentale utilità, sono i pannelli distribuiti lungo la linea di produzione, infatti hanno permesso di integrare, in formato digitale, tutte le attività di controllo qualità svolte durante il processo, generando report on-line e in tempo reale. Tutti i report così compilati vengono archiviati nel database centrale, con tutte le informazioni raccolte per ogni codice prodotto e per ogni lotto di produzione.
- I dati sono archiviati in tabelle specifiche all’interno di un database sul server aziendale e visualizzati su dashboard dedicate e personalizzate per le differenti aree e livelli aziendali:
- Il top management: con l’utilizzo dei principali KPI inerenti alla capacità produttiva generale;
- Gli indicatori di efficienza primari per le attività tattico-strategiche gestite a livello esecutivo (OEE, FTE);
- I KPI macchina: importanti per l’area qualità, la manutenzione e la produzione;
- Gli indicatori di processo: importanti per il controllo qualità (temperature, ph, % di sale).
I benefici
- Controllo dell’intero processo produttivo, dei servizi ausiliari e generali
- Incremento della performance produttiva
- Incremento della flessibilità produttiva
- Miglioramento della qualità di prodotto e di processo
- Riduzione di scarti e rilavorazioni
- Raccolta, storicizzazione e calcolo di diversi KPI
- Fruibilità delle informazioni ai differenti livelli aziendali
- Vantaggio Industria 4.0
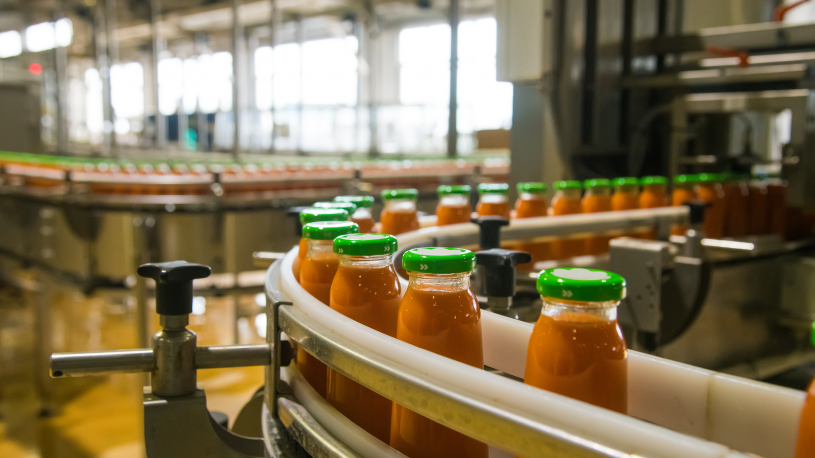