The client
Athena SpA is an Italian company, founded in 1983.
Over the years, Athena has become a world-wide provider of Single Pigment Concentration (SPC) for the master-batch manufacturing industry.
Athena has long-term experience in all matters related to pigments and pigment preparations, and is now specialized in the production of Single Pigment Concentrations based on inorganic and organic pigments.
The challenge
Athena started the transformation process in a digital factory, introducing a production progress monitoring system on the production line of the plant located in Vaprio d’Agogna, replacing the current solution based on paper orders and reports.
They need a flexible production system that manages the process, qualifying it in a documentable way and connected to the factory information system.
The solution
Cannon Automata supplied Connect-IT, the enabling solution for Industry 4.0 certification, able to adapt to the factory management system and to the existing line made up respectively of the following work centers: Mixing, Quality Testing, Extrusion, Cutting and Packaging.
Connect-IT carries out two fundamental integration activities and consists of two main stations:
- The PMS – Production Monitoring System, is the software interface to the existing MES of the customer from which one receives information on the order and production order, and to which the operator station communicates data at the end of the cycle.
- TOTEM I4.0, the intelligent station which, thanks to the DCSP-Data Collection Supervision Production software, interfaces with the PLC of the work station machines, to send production recipes and for real-time collection of productive data process.
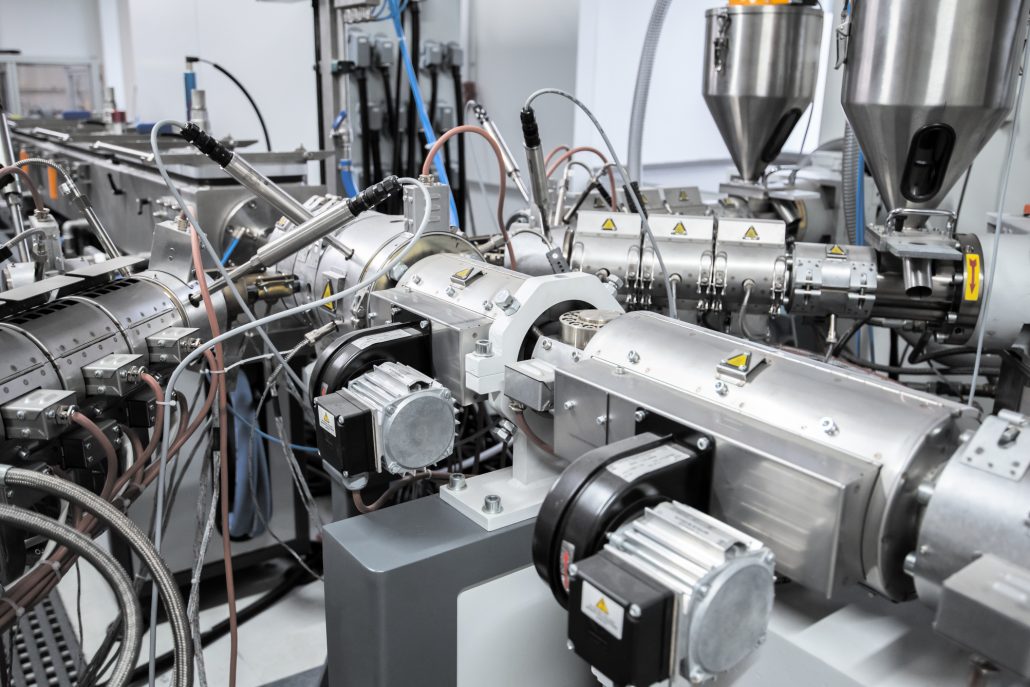
The phases of the production line managed and integrated by the Connect-IT solution:
Phase 1
The production order, coming from the management of a specific product, corresponds to a particular mixture and recipe. The production manager defines the number of compounds and completes the production order with the information required for the operator.
This information is sent from the PMS to the Mixing station and displayed on the screen by the operator.
Phase 2
At the end of mixing, the recipe is presented on screen and inserted on the extruder. When required, a sample is collected and it is generated its lab label.
Phase 3
The sample is recognized in the laboratory.
If at the end of the tests the result is positive, it goes to the next phase (In case of lack of approval, the laboratory will enter any changes and return to point 1 and 2).
Phase 4
Once the production cycle is complete and all the process data relating to the work center are collected, the information goes to the final step: cutting, bagging and final labeling of the product.
The benefits
- Improvement of production times and increase in productivity
- Improvement of process quality and flexibility
- Improvement of product quality
- Reduction of maintenance operations
- Information that can be used at various company levels
- Investment subject to tax benefits provided for by the Industry 4.0 plan.