Il cliente
Athena SpA è una società italiana, fondata nel 1983.
Nel corso degli anni è diventata fornitore mondiale di Single Pigment Concentration (SPC) per l’industria manifatturiera master-batch.
L’azienda ha una lunga esperienza nella preparazioni di pigmenti, in particolare è specializzata nella produzione di Single Pigment Concentrations (40-80%) a base di pigmenti inorganici e organici.
La sfida
Athena ha avviato un percorso di trasformazione in fabbrica digitale introducendo un sistema di monitoraggio di avanzamento produzione sulla linea produttiva dello stabilimento di Vaprio d’Agogna in sostituzione dell’attuale soluzione basata su ordini e report cartacei.
Un sistema di produzione flessibile che gestisca il processo, qualificandolo in maniera documentabile e connessa al sistema informatico di Fabbrica: flessibilità di macchina, flessibilità di produzione, integrazione al sistema logistico, tracciabilità dei dati di produzione, monitoraggio e storicizzazione dei dati.
La soluzione
Cannon Automata ha fornito Connect-IT, la soluzione abilitante per la certificazione Industria 4.0, in grado di adattarsi al sistema gestionale di fabbrica e alla linea esistente composta rispettivamente dai seguenti centri di lavoro: miscelazione, test di qualità, estrusione, taglio ed insacchettamento.
Connect IT svolge due attività di integrazione fondamentali ed è caratterizzato da due componenti principali:
- Il PMS-Production Monitoring System, il software di interfaccia verso il gestionale dal quale riceve le informazioni relative all’ordine di produzione e commessa e verso il quale la stazione operatore comunica i dati al termine del ciclo produttivo.
- TOTEM I4.0, la stazione intelligente che grazie al Software DCSP- Data Collection Supervision Production, si interfaccia verso il PLC delle macchine delle stazioni di lavoro, per l’invio delle ricette di produzione e per la raccolta in tempo reale dei dati del processo produttivo.
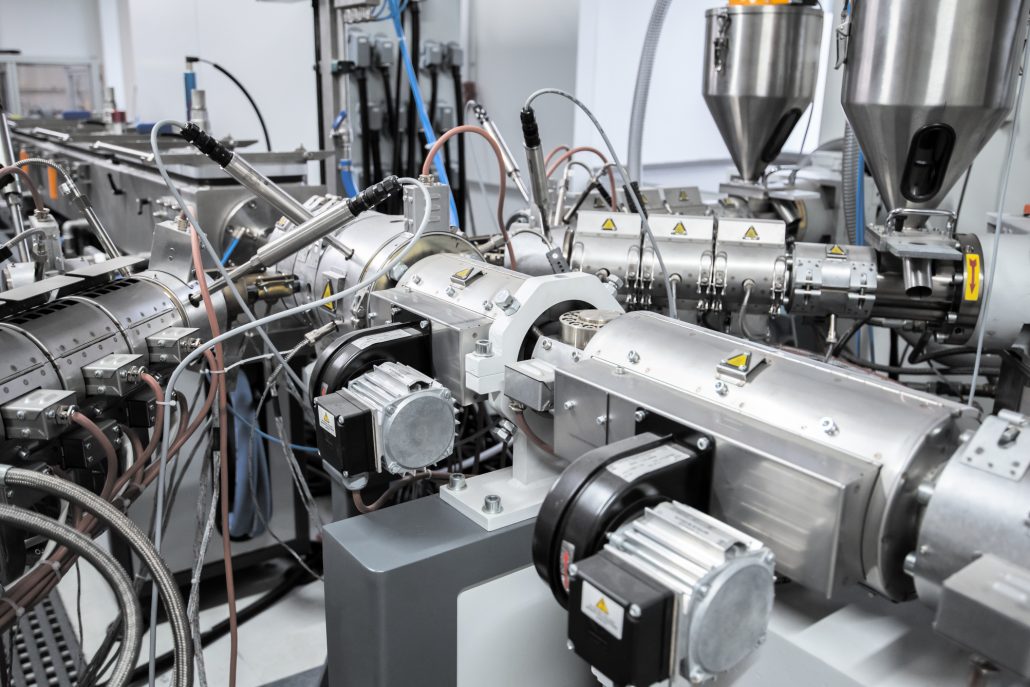
Le fasi della linea di produzione gestite ed integrate dalla soluzione di Cannon Automata:
Fase 1
Dal gestionale parte l’ordine di produzione dove ad uno specifico prodotto corrisponde una particolare miscela e ricetta. Queste informazioni vengono inviate alla stazione di miscelazione e visualizzate a video dall’operatore.
Fase 2
Al termine della miscelazione, la ricetta viene presentata a video e inserita sull’estrusore. Quando richiesto viene raccolto un provino e viene generata la sua etichetta per le prove di laboratorio.
Fase 3
Il provino viene riconosciuto in laboratorio. Se al termine delle prove l’esito è positivo, si passa alla fase successiva (in caso di mancata approvazione il laboratorio inserisce le eventuali modifiche e si torna al punto 1 e 2).
Fase 4
Una volta completato il ciclo produttivo e raccolti tutti i dati di processo relativi al centro di lavoro, le informazioni passano allo step conclusivo ovvero taglio, insacchettamento ed etichettatura finale del prodotto.
I benefici
- Miglioramento dei tempi di produzione ed incremento della produttività
- Miglioramento della qualità e della flessibilità di processo
- Miglioramento della qualità di prodotto
- Riduzione degli interventi manutentivi
- Informazioni più fruibili ai vari livelli aziendali
- Investimento soggetto ai benefici fiscali previsti dal piano Industria 4.0.