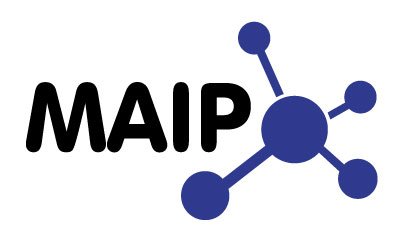
The client
Innovative solutions, eco-sustainable products, process quality and constant technical support. These are the features that distinguish Maip Group.
They have always been a leader in the plastics market.
Maip Compounding, a thermo-polymer and compounding manufacturer, develops a wide range of high-tech and environmentally friendly engineered thermoplastic materials.
The client is attentive to special colors and technical solutions requiring the development of customized filled and reinforced formulations.
The challenge
For the new operational headquarter in Settimo Torinese, Maip has chosen us as a strategic partner to supply factory integration solutions.
This significant and technologically advanced investment takes sustainability into account.
The main goals defined by MAIP are:
- Quality assurance, ie. continuous check-ups and traceability of materials used in all stages of production.
- Optimization and digitization of production process data, in accordance with delivery deadlines and punctuality.
- Acquisition of processing times of different phases and management of unavailability times of machines, allowing the operator to assign any cause of unavailability. From the collected data it is possible to carry out dedicated statistical analyses.
- Achieving a perfect balance between systems, machines and operators: a triple guarantee for the finished product and the client.
The solution
We supplied Connect IT, the hardware and software solution capable of creating perfect integration among the company’s centralized IT system, the operator interface and the machines, for order management and proper production progress.
Each production phase was equipped with the Totem I4.0 operator interface, a high-tech workstation capable of creating two-way communication between the management system and the machines in the field.
Let’s analyze in detail the process and the data managed, verified by our solution along the various production stations:
I – Raw materials warehouse
The polymers are stored in the RM warehouse. Each package is equipped with a QR code containing information on the material it contains, according to a format shared between the management system and the Automata solution. Every day the operator can view the list of materials, collected on a tablet, and check packaging’s compliance by scanning the QR code.
II – Throwing and weighing
The material coming from the warehouse is weighed and conveyed into special mixing silos.
Before releasing the polymer to the next step, a further check of the product is carried out by a QR reader.
III – Mixer
During mixing, two types of orders are managed:
- Premix orders: recipes with few ingredients and from which semi-finished polymers are obtained. At the end of the cycle, the material is further identified with a QR label.
- Extrusion orders: complex recipes, in which it is necessary to correctly dose polymers, additives and powders in precise percentages.
IV – Extrusion
During the extrusion phase, the system via Totem I4.0 displays and manages the accuracy of the ingredients used, the dispensers’ recipe and the extruders’ machine setpoints. Once this phase is completed, the material undergoes a further treatment inside the mixer to increase its homogeneity.
V – Bagging
Once the extrusion cycle is complete, the final step, packaging, takes place.
In this area the information regarding the material to be packaged, the machine used and the chosen packaging format is managed and verified.
A label with an identifying QR code is generated and printed.
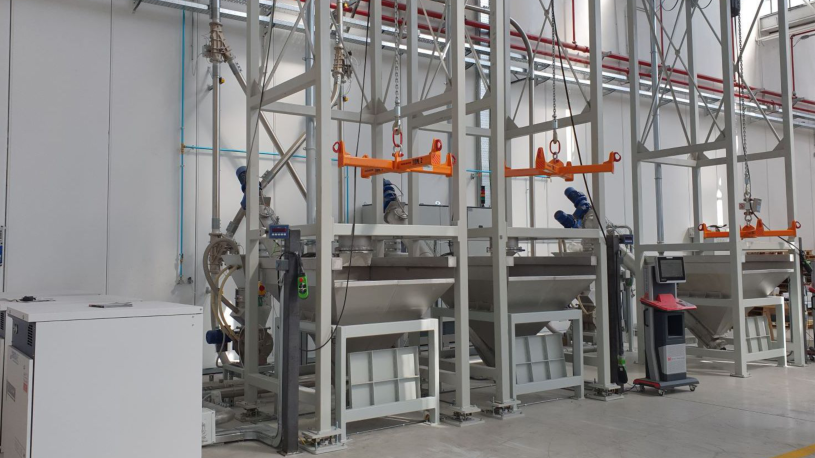
The benefits
- Fully interconnected and automated process;
- Improved product quality through continuous verification and material traceability through the various stages;
- Improved production times and increase of productivity;
- Improved of process quality and flexibility;
- Investment subject to Industrial 4.0 tax benefits.
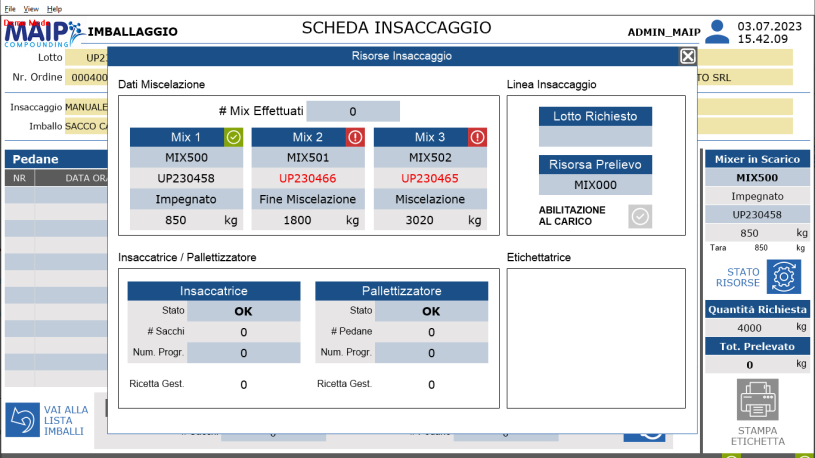